School of Mechanical Engineering
Cultivating Future-oriented Mechanical
Systems Engineers
The objective of School of Mechanical Engineering is to produce expert engineers of mechanical systems who utilize their knowledge of mechanical engineering constructively for the benefit of mankind and the environment. More specifically, the objectives of School of Mechanical Engineering are: First, to develop the problem-solving skills necessary to solve engineering problems; second, to develop the skills to expertly combine and use knowledge from different fields; third, to produce forward-looking experts who aspire to continuously advance the field of engineering; fourth, to produce engineers with leadership skills based on their experience with team projects; and finally, to produce competent engineers with expertise in the essential theories and practical applications of the field of mechanical systems engineering through education on dynamics, planning with computers, and various experimental training programs. Our graduates have completed the programs related to energy and environmental systems, robotics and nanosystems, and other mechanical systems that require both theory and practical application. Furthermore, they are entering into a wide array of fields and industries acting as a motive power for national growth, as well as working in research institutes.
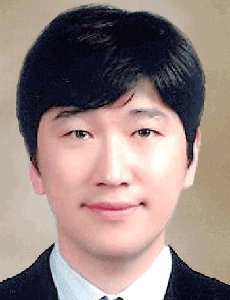
- Seoul National Univ., B.S.
- Seoul National Univ., M.S.
- Seoul National Univ., Ph.D.
- Heat Transfer
jahn@kookmin.ac.kr
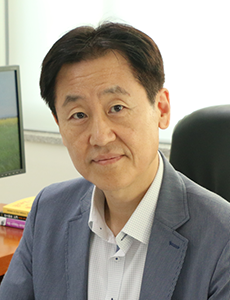
- Hanyang Univ., B.S.
- Hanyang Univ., M.S.
- Tokyo Institute of Technology, Ph.D.
- Intelligent CAD
cha@kookmin.ac.kr
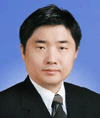
- Seoul National Univ., B.S.
- Seoul National Univ., M.S.
- Seoul National Univ., Ph.D.
- Refrigeration & Control
yschang@kookmin.ac.kr
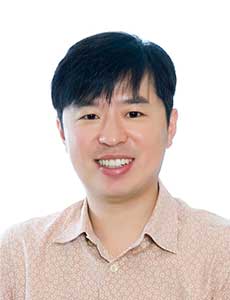
- KAIST, B.S.
- KAIST, M.S.
- KAIST, Ph.D.
- Robotics & Control
baekkyucho@kookmin.ac.kr
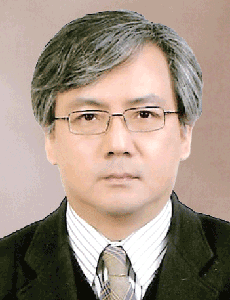
- Yonsei Univ., B.S.
- Yonsei Univ., M.S.
- Virginia Polytechnic Institute and State Univ., Ph.D.
- Fracture Mechanics, Elasticity
hjchoi@kookmin.ac.kr
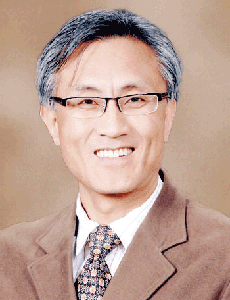
- Seoul National Univ., B.S.
- Seoul National Univ., M.S.
- Univ. of Minnesota, Ph.D.
- Heating, Ventilating and Air Conditioning
hhan@kookmin.ac.kr
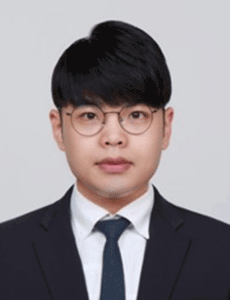
- Yonsei Univ., B.S.
- Seoul National Univ., Ph.D
- Fuel Cells, Hydrogen Generation
sjang@kookmin.ac.kr
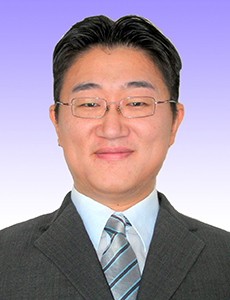
- Seoul National Univ., B.S.
- Seoul National Univ., M.S.
- Seoul National Univ., Ph.D.
- Robotics & Calibration
jayjeong@kookmin.ac.kr
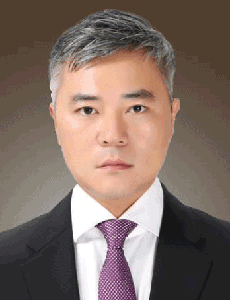
- Kookmin Univ., B.S.
- KAIST, M.S.
- KAIST, Ph.D.
- Laser Processing and Micro/Nano Engineering
bckang@kookmin.ac.kr
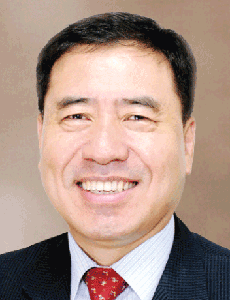
- Seoul National Univ., B.S.
- Seoul National Univ., M.S.
- Rutgers Univ., Ph.D.
- Applied Heat Transfer
bhkang@kookmin.ac.kr
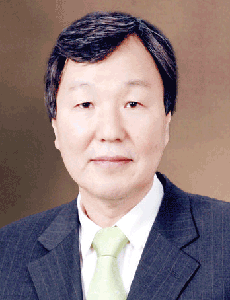
- Seoul National Univ., B.S.
- Seoul National Univ., M.S.
- Seoul National Univ., Ph.D.
- Computational Mechanics
ckim@kookmin.ac.kr
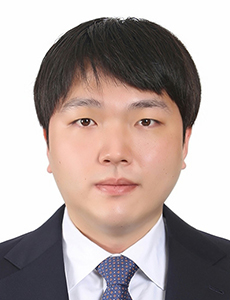
- Yonsei Univ., B.S.
- Yonsei Univ., M.S.
- Georgia Institute of Technology, Ph.D.
- Dry Adhesion, Surface Engineering
kimjaekang@kookmin.ac.kr
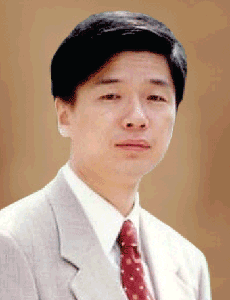
- Seoul National Univ., B.S.
- Seoul National Univ., M.S.
- Univ. of Michigan, Ph.D.
- Manufacturing Engineering
kim@kookmin.ac.kr
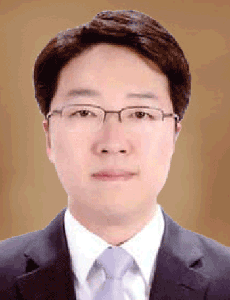
- Seoul National Univ., B.S.
- Seoul National Univ., M.S.
- Seoul National Univ., Ph.D.
- Biomedical Engineering
jkkim@kookmin.ac.kr
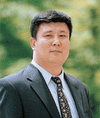
- Seoul National Univ., B.S.
- Seoul National Univ., M.S.
- Purdue Univ., Ph.D.
- Manufacturing Engineering
kangkim@kookmin.ac.kr
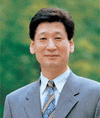
- Seoul National Univ., B.S.
- Seoul National Univ., M.S.
- UCLA, Ph.D.
- Thermal Engineering
skim@kookmin.ac.kr
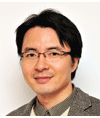
- Hanyang Univ., B.S.
- Hanyang Univ., M.S.
- Texas A&M Univ., Ph.D.
- Mechanical Design & Vibration Control
thk@kookmin.ac.kr
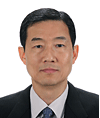
- Hanyang Univ., B.S.
- Pennsylvania State Univ., M.S.
- Pennsylvania State Univ., Ph.D.
- Composite Materials, Design
twkim@kookmin.ac.kr
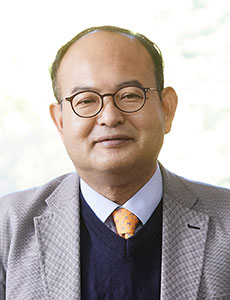
- Seoul National Univ., B.S.
- Seoul National Univ., M.S.
- Seoul National Univ., Ph.D.
- Mechanical Design Engineering
calif@kookmin.ac.kr
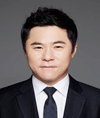
- KAIST, B.S.
- KAIST, M.S.
- Carnegie Mellon University, Ph.D.
- Two-phase Thermal Flow
joellee@kookmin.ac.kr
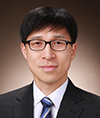
- Seoul National University, B.S.
- Seoul National University, M.S.
- Georgia Institute of Technology, Ph.D.
- Sustainable Energy
hyunjinlee@kookmin.ac.kr
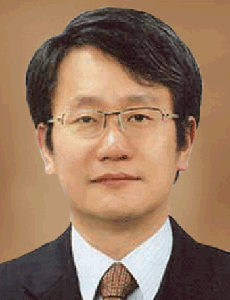
- Hanyang Univ., B.S.
- KAIST, M.S.
- KAIST, Ph.D.
- Micro/Nano/Bio System
keeslee@kookmin.ac.kr
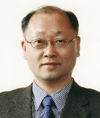
- Seoul National Univ., B.S.
- Technical Univ. of Berlin, M.S.
- Technical Univ. of Berlin, Ph.D.
- Design Methodology
kslee@kookmin.ac.kr
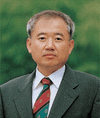
- Seoul National Univ., B.S.
- KAIST, M.S.
- Cornell Univ., Ph.D.
- Computational Plasticity and Microforming Processing
yslee@kookmin.ac.kr

- Seoul National Univ., B.S.
- Seoul National Univ., M.S.
- UC Berkeley, Ph.D.
- MEMS/NANO
shlim@kookmin.ac.kr
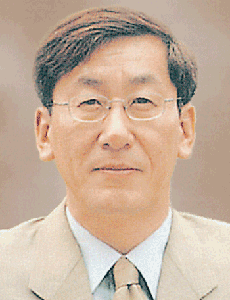
- Seoul National Univ., B.S.
- KAIST, M.S.
- Univ. of Tokyo, Ph.D.
- Computational Fluid Dynamics
myong@kookmin.ac.kr
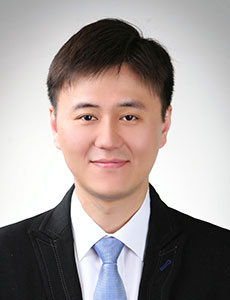
- Univ. of California, Berkeley., B.S.
- Univ. of California, Berkeley, M.S.
- Univ. of California, Berkeley, Ph.D.
- MEMS/Nano
koonam@kookmin.ac.kr
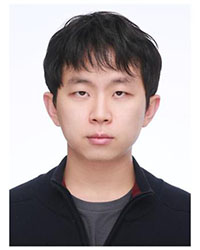
- Seoul National Univ., B.S.
- Seoul National Univ., M.S.
- Seoul National Univ., Ph.D.
- Mechanical and Aerospace Engineering
parkjo05@kookmin.ac.kr
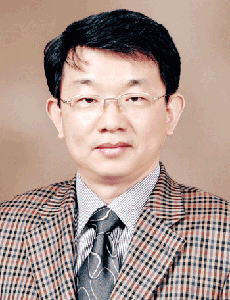
- Seoul National Univ., B.S.
- KAIST, M.S.
- Univ. of Michigan, Ph.D.
- Thermodynamics
pkk@kookmin.ac.kr
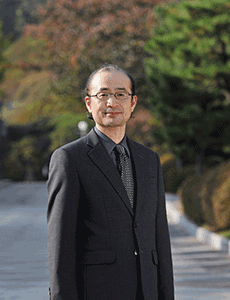
- KAIST, B.S.
- KAIST, M.S.
- KAIST, Ph.D.
- Mechanical Engineering
d.shin@kookmin.ac.kr
Basic Courses
Statics (3)Basic concepts of Newton’s law, moment, couple, resultant, equilibrium, centroid, centers of gravity, analysis of structures, forces in beams and cables, friction, moments of inertia in areas moments of inertia in masses, and the method of virtual work are covered in this course.
Introduction to Mechanical Systems Design Ⅰ (3)
Applied Engineering Mathematics Ⅰ(3)This course describes application of differential equations in engineering. Topics include ordinary differential equations, Laplace transform, Fourier series, partial differential equations, integration in the complex plane, and conformal mapping.
Introduction to Mechanical Systems Design Ⅱ (3)
Computer.Aided Mechanical Drafting (2)This course provides fundamental theory in engineering drawing for expressing designer’s intent. Topics include orthographic projection, dimensioning, sectioning, exploded and auxiliary views, and assembly drawings.
Applied Engineering Mathematics Ⅱ(3)This course helps students to apply mathematics to solve real-world problems dealing with probability, statistics, and data analysis. Topics include descriptive statistics, probability models and related concepts and applications, statistical estimation, and hypothesis testing.
Introduction to Mechanical Systems Design Ⅲ (3)Major Courses
C Languages (3)This course studies problem solving methods and procedures using computer. Based on fundamental knowledge on computer hardware and software, the function and usage of C programming language are studied.
Thermodynamics (3)This course helps in understanding the role of thermodynamics on mechanical engineering. Definitions and basic concepts of thermodynamics, properties of pure substance, work and heat, the first law of thermodynamics, system and control volume, steady-state flow processes, heat engines and refrigerators, reversible processes, the second law of thermodynamics, entropy, and cycle efficiency are described in this course.
Introduction to Electrical and Electronic Engineering (3)This course covers fundamental theories in the electrical and electronic engineering that are required for mechanical and automotive engineers. The topics include fundamentals of electric circuits, resistive network analysis, equivalent circuits, AC network analysis, frequency response, amplifiers, and digital logic circuits.
Fluid Mechanics (3)This course describes the field of applied mechanics concerned with the behaviors of liquids and gases at rest or in motion. Some experimental and theoretical analysis will be included to explain fluid behaviors. In the field of theoretical analysis to describe the fluid behaviors, mathematical formulations which are based on the principles of mass conservation and Newton’s second law are covered. To fulfill the objective of this course, basic concepts of fluid mechanics are applied to real problems.
Engineering Materials (3)This course gives an introduction to the materials and their properties in mechanical engineering applications. Processing, structure and property relations in engineering materials such as metals, ceramics, polymer and composites are main topics covered in this course.
Mechanics of Materials (3)The mechanics of deformable solids in equilibrium which exhibit mainly the elastic behavior is taught. Specifically, the important concepts of stresses and strains are first introduced, followed by the analyses of various structural members subjected to axial loads, torsion, and bending moments in order to determine the deformation modes and the corresponding stresses produced under such external loading conditions. The design projects are to be conducted and presented by the students at the end of this course.
Dynamics (3)Dynamics of particles history of dynamics, dimensions, rectilinear motion, plane curvilinear motion, rectangular coordinates, normal and tangential coordinates, polar coordinates, space curvilinear motion, relative motion, Newton’s second law, work and kinetic energy, potential energy, linear impulse and linear momentum, angular impulse and angular momentum, impact, central.force motion. Dynamics of rigid bodies rotation, absolute motion, relative acceleration, motion relative to rotating axes, general equations of motion, translation, fixed.axis rotation, general plane motion, work.energy relations and impulse.momentum equations.
Applied Thermodynamics (3)The second law of thermodynamics, various power cycles, refrigeration and air conditioning systems, compressors and gas turbines and chemical reactions are studied. Based on these theories, the design of thermodynamic systems is carried out to solve practical engineering problems.
Applied Mechanics of Materials (3)This course is a continuation of the prior prerequisite to solid mechanics, focusing on the applications of basic concepts and principles of solid mechanics to various engineering materials and structures. Following a brief but overall review on the fundamentals of solid mechanics, the topics covered are transverse shear effects, combined loads, three-dimensional constitutive relations, stress-strain transformations, design and deflection of beams and shafts, buckling and stability of columns, and energy methods. The students should conduct the design projects and present the results before the end of this class.
Mechanism Design (3)This course fowson the velocity, acceleration of moving parts in machine elements and mechanisms using graphical and analytical techniques. Topics covered include use of vector, graphical, and matrix methods for kinematic analysis, introduction to graphical and computer methods for kinematic synthesis of mechanisms, linkage systems, cams, gears, gear train design, and analysis.
Heat Transfer (3)The basic modes of heat transfer, such as conduction, convection and radiation are considered in this course. The multiple dimension of steady state conduction, unsteady state conduction, the numerical analysis of heat conduction, the principle of convection heat transfer, and forced convection heat transfer are studied in this course. Heat sink design is carried out using the combined heat transfer modes of conduction, convection and radiation.
Manufacturing Process (3)An introduction to conventional manufacturing processes casting, metal forming, cutting, grinding, welding, and the influence of the process on the final mechanical properties of a product. Emphasis is on the practical applications with various examples.
Applied Fluid Mechanics (3)This course covers viscous flow in pipes including Hagen-Poiseuille flow, drag and lift by flow over immersed bodies, boundary layer analysis, differential analysis of fluid flow, potential flow, and fluid flow measurement. A brief introduction to open channel flow and compressible flow are provided in case time permits.
Automatic Control (3)Introduction to classical control theories for linear dynamic systems. Modeling and linearization of dynamic systems. Root locus and frequency response design methods. Compensator design for designed performances.
Mechanical Engineering Elements Design (3)A beginning course in mechanical engineering design a review of the mechanics of materials, engineering materials, failure theories, and the design of mechanical elements (screws, keys, pins, joints, welding, and adhesive bonding).
Applied Mechanical Engineering Elements Design (3)The second course in mechanical engineering design design of mechanical elements as applied to machines and automotives (springs, bearings, brakes, gears, flywheels, and design applications).
Experiments in Mechanical Systems Engineering Ⅰ (2)The principles and advanced techniques in mechanical and automotive engineering are explored in brief lectures and experiments. Topics include operation and performance experiment of various apparatus in thermal and fluid engineering mechanical vibration material mechanics (elastic and plastic) material test applied mechanics experiment vehicle suspension simulator shock absorber experiment steering system simulator vehicle harshness and vibration experiment vehicle safety experiment pneumatic control experiment vehicle drivetrain system simulator thermal and fluid engineering experiment electrical apparatus experiment.
Manufacturing Process Lab (1)Practice of basic manufacturing processes (turning, milling, drilling, welding, measurement, etc.) to get the knowledge of machine tool characteristics and basic operations.
Mechanical Vibration (3)Free and forced vibrations, with damping, of linear systems with one-, two. and multi-degree of freedom. Transient vibrations. Vibration measurement and evaluation. Vehicle vibration analysis.
Numerical Analysis (3)This course is intended to introduce the theories and methods that are required when finding the approximate solutions to various engineering problems of practical importance. Topics including error analysis, roots of equations via bracketing and open methods, Gauss elimination, LU decomposition, matrix inversion, curve fitting methods involving regression and interpolation, numerical differentiations, and various numerical integration formulas are covered.
Finite Element Method (3)This course introduces the basic concepts and theories such as direct stiffness method, energy method, Galerkin’s weighted residual method for finite element formulation. Applications to stress analyses and structural analyses are practiced with an educational Finite Element package.
Computer-Aided Design (3)Fundamental theory and practical aspects of CAD system are explored. Topics include introduction to computer graphics basic freeform curves, and surfaces solid modeling systems feature.based parametric design standard data exchanges mesh generation.
Intelligent CAD (3)This course covers the existing CAD theory and system, and discusses functions and items necessary to realize the intelligent CAD system. This course discusses Artificial Intelligence, Virtual Reality, Distributed Design Environment, and the latest CAD technology.
Computer Aided Manufacturing (3)Introduction to the use of the digital computer as a tool in manufacturing engineering. Special consideration is given to geometric modeling, umerical-control programming, programmable logic controllers, industrial robotics, group technology, process planning, and integrated computer aided manufacturing. Three one-hour lectures per week and NC programming laboratory.
Micro Thermal-Fluid Dynamics (3)This course is intended to provide the foundation of thermo-fluid mechanics. Topics include hydrostatic waves, the Navier-Stokes equation, miscellaneous topics in thermodynamics, and flow with heat transfer.
Internal Combustion Engines (3)An introduction to the automotive internal combustion engines thermodynamics, fluid dynamics, mechanics of materials, and the influence of performance and exhaust gas properties. Emphasis is on the practical applications with various examples.
Robotics (3)Introduction to the fundamental principles of robot engineering. Although this course covers a fair amount of robot manipulator’s mechanics, kinematics, dynamics, position and force control, and trajectory planning, it also covers the application of actuators and sensors which are the basic components of robot system. Finally student can learn the principles of microprocessor through making a small robot as line tracer system.
Mechanical Behavior of micro/nano System materials (3)Fundamental theories and advanced technologies are introduced for the recent developed nano-micro precision actuators and measurement systems. The nonlinear characteristics of the integrated micro.nano systems is also covered and their applications lay on the designs and concepts of micro.nano actuator and measure ment systems, semiconductor fabrications and manufacturing equipments, optical measurement systems, scanning probe microscopes and micro.nano tribology systems.
Mechanical Measurement (3)Principles of measurement with digital sampling and spectrum analysis are introduced and measurement methods for distance, time, velocity, force and pressures are lectured in this course. In order to exercise the spectrum analysis of digitally sampled data, data acquisition softwares such as Labview, Matlab and Methmatica are used in this course. Some experimental micro-nano optic measurements of gap distance are also introduced for the real measurement skills.
Mechatronics Systems Design (3)Discussion of various electronic control systems for intelligent vehicles, advanced safety vehicles and driver assistance systems. Design and evaluation of vehicle control algorithms. method, which is based on the vehicle dynamics. The course covers the following topics fundamental theory for vehicle dynamics, cornering compliance concept, optimization of Ride & Handling characteristics, kinematic design of suspension and steering system, compliance design component and structure design.
Strength and Fracture of Materials (3)The failure behaviors of engineering materials and structures are studied from the standpoint of strength and fracture of materials in order to gain relevant concepts and knowledge that are useful in understanding the failure causes and preventions. In this regard, various conventional failure models and criteria are reviewed and the deformation modes due to the existence of crack-like defects are introduced, introducing the concepts of crack driving forces and fracture toughness. The fatigue behavior of engineering materials with and without the cracks and the method to predict the corresponding fatigue life are also dealt with.
HVAC (Heating, Ventilating, and Air Conditioning) (3)Topics include theories and applications of psychrometrics, load calculation, air conditioning/planning, as well as HVAC equipments, piping & duct design for a building. Joining a practice HVAC design is a mandatory for students. Completing this course, a student should be capable of participating in the design of a basic HVAC system.
Heat Engine (3)This course provides the fundamentals of steam power station including characteristics of steam cycle and steam boilers, fuels and combustion, steam turbines, steam engines, condenser, and nuclear power plant.
Materials and Design (3)Scientific and industrial design basis for material selection problems in engineering design. Case studies may include concepts for automotive or aerospace composite structures, electronics, sporting goods, micro-nano structures, and bio-materials.
Energy and Environmental Engineering (3)The theories, methods, and problems at realization of the new and renewable energy sources are lectured, which include fuel cell, geo-thermal energy, solar energy, biomass, small hydraulic energy, tidal energy, wind power, coal and crude oil gasification, refuse energy, and hydrogen.
Plant Engineering (3)Engineering methods and management technology for plant design, construction, and operation are lectured, which include energy and power plant, environmental plant, chemical plant, etc.
CFC (Computational Fluid Dynamics) (3)Training course to experience design and analysis for heat transfer and fluid flow with educational CFD(Computational Fluid Dynamics) package, Emphasis is on practical applications with various examples.
Turbomachinery (3)This course deals with energy and angular momentum considerations of turbomachines such as axial and centrifugal fans, pumps, compressors, turbines, and watermills and windmills. Emphasis are given to basic design practices using scaling law, specific speed, net positive suction head, and pump performance and system characteristics in practical fluid system applications.
Fluid Power System (3)Introduction to hydraulic and pneumatic systems. Various components of fluid power systems. System and control design for designed performances.
Mechatronics Design (3)This course provides mechatronics issues using simple examples of mixed electro mechanical systems. Starting with theoretical background and followed by illustrative numerical problems, we can practice the real automotive industry application problems. Finally it explores all major topics in mechatronics and offers the computer simulation devices such as LabVIEW application.
Manufacturing Automation (3)Study on the technology by which a process or procedure is accomplished without human assistance. Emphasis is on automation, industrial computer control, control system components, numerical control, industrial robotics, and programmable logic controllers.
Concurrent Engineering (3)Introduces the concept and history of concurrent engineering, and improves the product design and the manufacturing process from the view point of concurrent engineering, and cultivates practical usage of this engineering methodology through case studies and analysis using S/W (DFA, DFM).
UROP (3)
Computational Mechanics (3)
E-Biosystems (3)
Mechanical Systems Engineering SeminarⅠ,Ⅱ (3)
Creative Thinking (3)
Experiments in Mechanical Systems Engineering (3)
Special Topic in Mechanical Systems Engineering Ⅰ,Ⅱ (3)
Education Courses
Theories of Teaching in Mechanical & Materials Engineering Education (2)Various subjects on teaching technical high school students in mechanical engineering, such as history or the effectiveness of mechanical engineering education.
Text Research and Teaching Methodology in Mechanical and Materials Engineering Education (2)Development of teaching materials and effective teaching methods for automotive engineering education at the industrial high school level.
Capstone Design Courses
Capstone Design I, II (3)The Capstone Design proposes a practical and innovative engineering education which covers creating concrete ideas, making designs, doing simulations and manufacturing the final products for General industrial and Automobile machines. The participants for this course learn how to apply engineering design consideration such as robustness and stability and practice team.based manufacturing so as to realize the design.
Interdisciplinary Capstone Design Ⅰ,Ⅱ (3)
Capstone Design for start-up